Automatic Lubrication Systems
Automatic Lubrication Systems are important to make it easy, safe and efficient to grease moving parts, during the machinery’s operation.
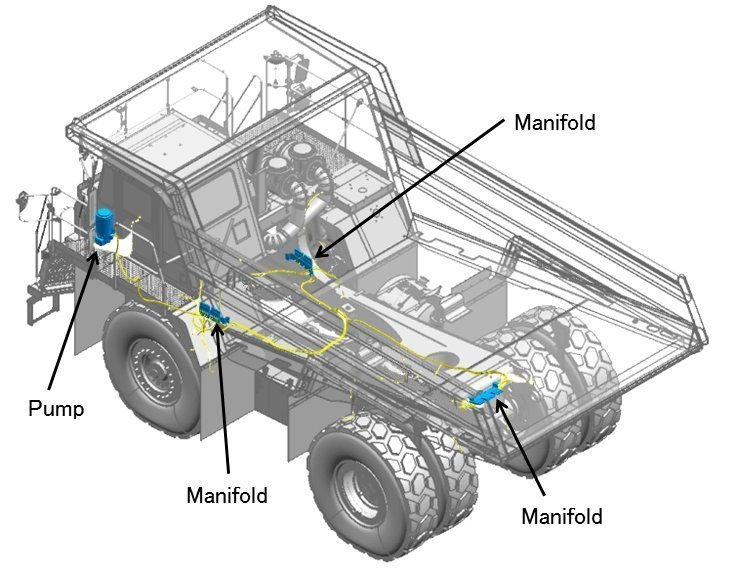
Automated lubrication systems for fixed plant equipment
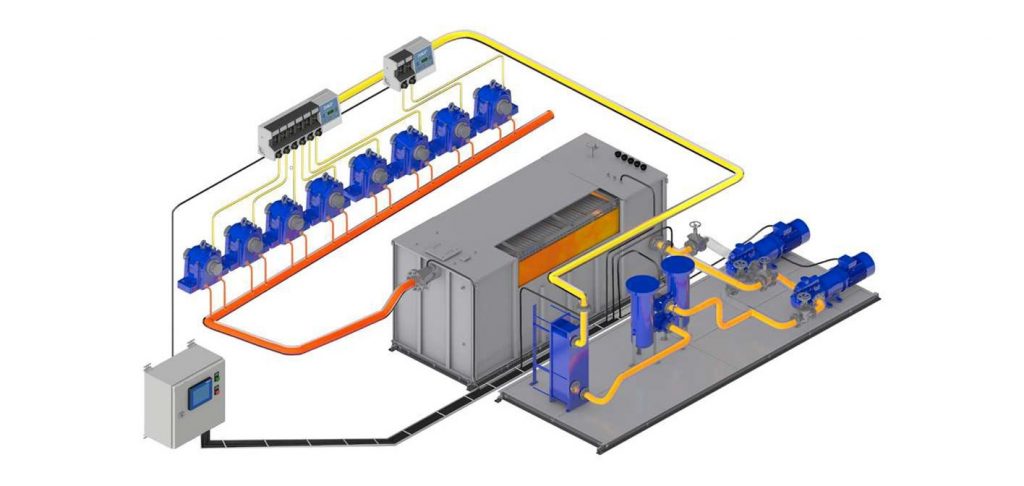
Amet Industries offer the complete portfolio of automatic lubrication systems and components. This broad product line includes both oil and grease-based systems. They can be off-the-shelf or customised for virtually every Industrial application.
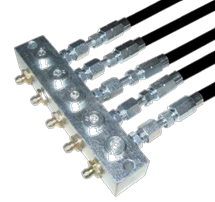
Remote Grease Line Lubrication
Automatic Lubrication on grease lines, is commonly known as Remote Grease Line Lubrication
Read More
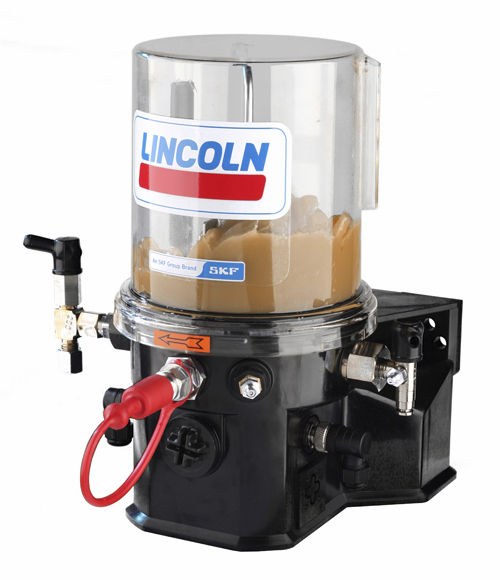
Lincoln Automatic Lubrication
Lincoln Lubrication Systems, provide the appropriate lubrication quantity at the correct intervals, minimising friction and wear and optimising bearing and machinery service life.
Read More
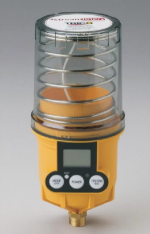
Trico Grease Lubrication
The lubrication of moving parts is critical to the protection and wear of metals when oil is not thick enough. Single-point and multi-point lubrication systems work together to keep bearings and other moving parts lubricated properly.
Read More
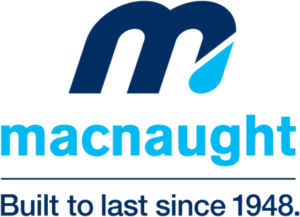
Macnaught Lubrication
Macnaught products, perform fluid measurement, fluid transfer and lubrication of equipment. Macnaught Lubrication systems are used in, the agricultural, automotive, industrial, mining and transport industries across the globe.
Read More
Lubrication Line Systems Available
Single Line Systems
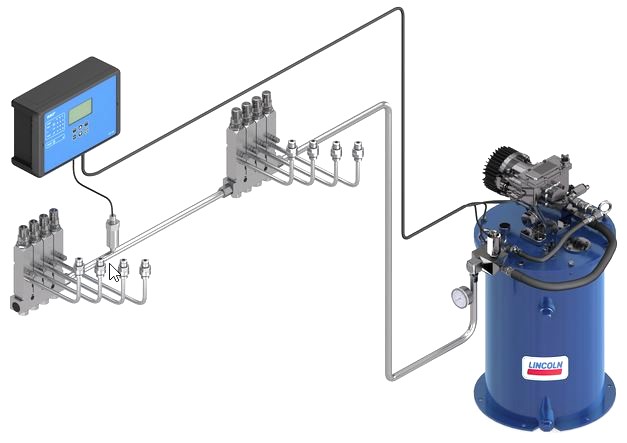
This includes both Mono Flex and CentroMatic system components including pumps, metering units, control and monitoring devices and accessories.
Regardless of the application, the principle of single-line lubrication remains the same.
A central pump station automatically delivers lubricant through a single supply line to the lubricant metering device. Each metering device serves only one lubrication point. It can be adjusted to deliver the precise amount of grease or oil required. Systems can service one machine, different zones on one machine or even several separate machines.
Advantages
- Integrated system control and monitoring
- Able to pump long distances and within a wide temperature range
- Easy to understand, install and maintain.
- Available in both preset and adjustable models
- Suitable for almost all lubricants
- Easy system expansion
- System continues to operate if one point becomes blocked
Dual Line Systems
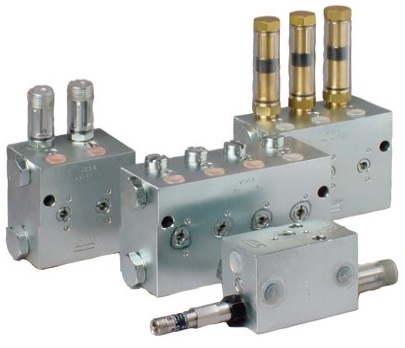
The dual-line, automatic lubrication systems, are designed for large machines with many lubrication points, long lines and harsh operating conditions. Typical applications include heavy industry, metal working plants, pulp and paper, mining, mineral processing and cement factories, deck cranes, power plants, sugar mills and more. These systems utilize two main lines that are supplied alternately with lubricant.
Advantages
- Parallel metering device setup enables simple system design
- Ideal for many lubrication points over long distances
- Very reliable when using high viscosity greases
- Flexibility in adjusting metered quantity
Smart lubrication
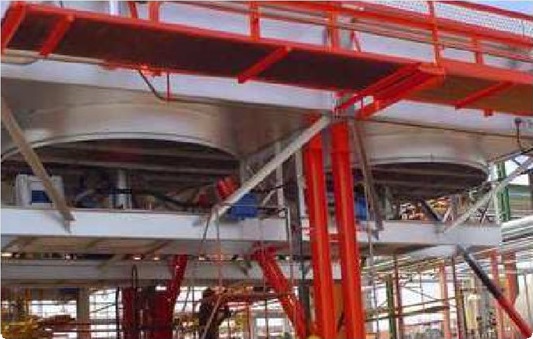
Compressors in hydrocarbon processing facilities fit into one of three categories:
1. Centrifugal compressors which must endure high speeds and temperatures.
2. Reciprocating compressors, used in low-volume, high- pressure applications.
3. Screw compressors used to distribute natural gas through pipelines under harsh chemical conditions.
Proper lubrication protects your compressor, extends the life of its critical components and keeps this valued asset generating revenue. Amet Industries has the experience and product portfolio for these lubrication tasks.
Delivering the right amount of oil at the right time to compressor cylinders and rod packing is a critical requirement to keep a natural gas compressor operating efficiently. Under-lubrication can cause damaging metal-to-metal contact that generates excessive heat and results in wear or machine downtime.
Over-lubrication essentially wastes money and negatively impacts compressor efficiency and the environment.
Lubricating and cooling at the same time.
Circulating oil lubrication is an electrically operated oil pumping, cooling and filtration system. It removes contamination and allows to condition oil temperature and contributes greatly to optimum lubrication with correct oil viscosity.
There are three different Circulating oil lubrication models available:
without Cooler
with Air Cooler
with Water Cooler
All models work in a side stream (kidney loop) configuration. The units are installed directly on the machine. Access ports should be located on opposing sides of the oil sump, so that suitable oil circulation is possible. Once installed the system is ready for continuous operation.
Features and benefits:
- Continuous lubricant cooling and filtration to extend machine life.
- Eliminates wear and premature failures efficiently
- Optional available with frequency converter, electrical clogging indicator, temperature transmitter, pressure transmitter, gauge, shut-off valve, flow meter, moisture transmitter or thermostat.
- Dust proof cabinet with cooling or heating design on request
- Virtually maintenance free
- Easy to use and install
Heavy loaded bearings on top drives, gearboxes or very large motors need special attention. The solution is a circulating oil lubrication system that separates dirt particles, air bubbles and water from the oil. A pressurized oil system transports the lubricant to the individually adjustable low meters. In case of cold external temperatures, an electrical heater can be used to provide optimal start up temperature in the lubrication cycle.
Customer Specific Solutions for Automatic Lubrication Systems
Customer-specific solutions are compact lubrication units in a pump-cooler arrangement. These units supply lubrication points with the right amount of tempered lubricating oil. The units are constructed with durable materials, to help ensure that even difficult temperate / dangerous conditions, have no negative effect on the system’s functionality.
Delivery rates can be monitored Visually or Electronically.
Multiple warning levels are available for condition-based maintenance.
Amet Industries offer, circulating oil lubrication systems, in a wide range of tailored and ready-to-use solutions (relative for volumetric lows from 1 to 3,000 l/min (0.26 to 792 gal/min)).
The number and type of units are determined by the lubricant used and its viscosity index, the required volume and the required pressure. Gear, gyrator and screw pumps are often used with these systems.
explosive atmospheres
AMET INDUSTRIES circulating oil lubrication systems can be used in explosive atmospheres.
– up to ATEX zone 1, or in compliance with relevant standards such as the American Petroleum Institute’s (API) Standard 614.
The BENEFITS of Automatic Lubrication Systems
PRODUCTIVITY – Improved Machine Productivity. Automatic lubrication systems help to improve machine productivity by reducing downtime and the need for manual lubrication. This can result in machines running more efficiently and for longer periods of time.
LESS MAINTENANCE – Substantially increase pin & bushing life, reducing the number of repairs required over the machine’s lifespan.
REDUCE CONSUMPTION – Automated lubrication systems reduce lubricant waste by only dispensing the exact amount of lubricant needed for the job. This prevents over-lubrication and helps to reduce costs.
ENHANCED RELIABILITY – Automatic lubrication systems help to ensure reliable lubrication of machines. This improves their performance and reduces the chances of breakdowns and other costly repairs.
INCREASE SAFETY – Automatic lubrication systems reduce the risk of workplace injuries caused by manual lubrication methods. This increases the safety of workers in the area and reduces the potential for accidents.
PAYS FOR ITSELF – The cost to replace one pin & bushing can pay for an Automated Lubrication System.
IMPROVED EFFICIENCY – Automated lubrication systems help to improve efficiency by reducing the time required to change and apply lubricant. This can result in lower labor costs and improved equipment performance.
RESALE – Improve resale by keeping your equipment in good working order.